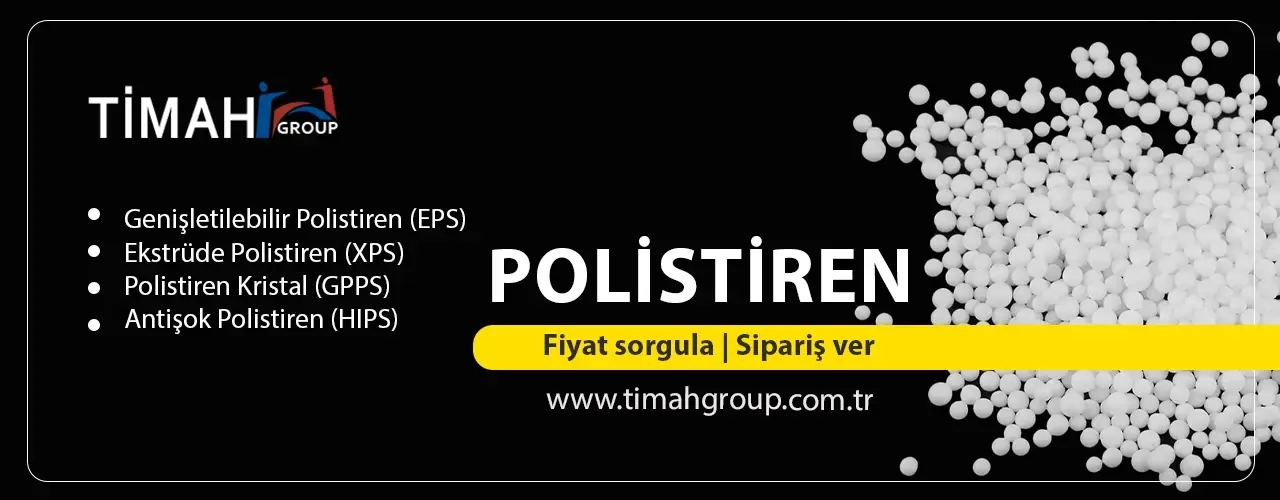
Types of Polystyrene and Their Applications
Expandable Polystyrene (EPS)
Expandable Polystyrene, commonly referred to as EPS, is a lightweight, rigid, and closed-cell foam material. EPS is known as a low-density thermoplastic material formed by heating polystyrene beads, which expand and bond together to create foam sheets or blocks.
Types of Expandable Polystyrene (EPS):
- 121HS
- 221HS
- 321HS
- 422 FC
- 522FC
- 526WP
- EPS F100
- EPS F150
- EPS F250
- EPS F350
- EPS F50
Features of EPS
- High Thermal Insulation: EPS has excellent thermal insulation properties, making it a widely used insulation material in buildings to improve energy efficiency.
- Lightweight: Due to its low density, EPS is easy to transport and install, making it an ideal material in the construction and packaging industries.
- Durability: EPS is resistant to moisture and chemicals, ensuring long-term durability. It is also resistant to deformation.
- Cost-Effective: EPS is a low-cost material, providing an economical solution even for large-scale projects.
Applications
- Construction Industry: EPS is used for roof, wall, and floor insulation in buildings. Its high thermal insulation properties help reduce energy costs.
- Packaging Material: EPS is commonly used as protective packaging for safely transporting delicate products.
- Decorative Products: Thanks to its lightweight and moldable properties, EPS is used in various decorative products.
- Engineering Fill Material: EPS is preferred as a fill material in road and railway projects.
Advantages
- Eco-Friendly: EPS is 100% recyclable and contributes to energy conservation.
- Fire Resistance: EPS products with flame-retardant additives offer a certain level of fire resistance.
- Versatile Application: EPS can be produced in various thicknesses and densities, making it suitable for a wide range of applications.
Expandable Polystyrene (EPS) is an indispensable material in the construction and packaging industries due to its economic and functional benefits. Its lightweight, insulation properties, and durability make EPS an ideal choice for modern construction and manufacturing projects.
Extruded Polystyrene (XPS)
Extruded Polystyrene, abbreviated as XPS, is a rigid, high-performance insulation material with a closed-cell structure. XPS is produced by an extrusion process, where polystyrene polymer is heated, melted, and then continuously extruded into sheets. As a result, XPS forms a strong, homogeneous material with a tight cell structure, offering excellent insulation properties.
Features of XPS:
- High Thermal Insulation: XPS provides excellent thermal insulation performance. Its low thermal conductivity makes it a popular choice for improving energy efficiency in buildings.
- High Compression Strength: XPS offers high compression resistance, making it ideal for sub-floor applications, roof coverings, and structures bearing heavy loads.
- Low Water Absorption: The closed-cell structure of XPS makes it almost impermeable to water, making it a long-lasting material in damp or water-exposed areas.
- Lightweight: Although lightweight, XPS is highly durable, allowing it to be easily transported and processed.
Applications:
- Roof and Wall Insulation: XPS is used for insulation in roofs, walls, and foundations of buildings. Its high insulation performance helps reduce energy costs and improve indoor comfort.
- Floor Insulation: XPS is preferred for sub-floor applications due to its high compression resistance and low water absorption properties.
- Exterior Cladding: XPS offers both aesthetic and functional solutions for exterior cladding, providing thermal insulation and protecting the building from external factors.
- Cold Storage Facilities: In cold storage, XPS’s high insulation capacity ensures temperature control.
Advantages:
- Energy Efficiency: XPS contributes to energy savings due to its low thermal conductivity, resulting in long-term cost savings.
- Environmental Durability: XPS is resistant to chemicals, moisture, and mold, offering a long-lasting insulation solution.
- Easy Application: Its lightweight and easy-to-process nature makes XPS a convenient material to use in construction projects.
Extruded Polystyrene (XPS) is widely used in the construction industry for its superior insulation properties and durability. It is an ideal insulation material for projects seeking to improve energy efficiency.
General Purpose Polystyrene Crystal (GPPS)
General Purpose Polystyrene Crystal, commonly known as GPPS, is a transparent, rigid, and brittle thermoplastic material. GPPS is produced by polymerizing the monomer form of polystyrene and is often characterized by its glass-like clarity. Due to these properties, GPPS is frequently used in applications requiring aesthetic appeal and visual clarity.
Types of General Purpose Polystyrene Crystal (GPPS):
- GPPS 1038
- GPPS 1077
- GPPS 1115
- GPPS 1160
- GPPS 1460
- GPPS 1540
Features of GPPS:
- Transparency: GPPS has a glass-like clear structure, making it ideal for applications requiring optical clarity.
- High Rigidity: GPPS offers high rigidity and low elasticity, making it a hard but brittle material.
- Low Density: Its low density makes GPPS advantageous for lightweight structural applications.
- Easy Processability: GPPS can be easily processed using injection molding, extrusion, and thermoforming, making it ideal for various industrial and consumer products.
- Cost-Effective: GPPS is more economical compared to other engineering plastics.
Applications:
- Food Packaging: GPPS is widely used in food packaging, including disposable containers and transparent packaging materials.
- Consumer Products: Commonly used for office supplies, CD/DVD cases, toys, and other everyday consumer products.
- Electrical and Electronics: GPPS is used in housings for electrical equipment and transparent parts of certain electronic devices.
- Decorative Products: Due to its transparent and glossy surface, GPPS is also used in decorative products.
Advantages:
- Aesthetic Appeal: The transparent and glossy surface of GPPS makes it an attractive option for applications where visual quality is important.
- Easy Processing: GPPS is easy to process and mold, allowing for a wide range of applications.
- Economical Solution: Its low cost makes GPPS an attractive material for large-scale production and consumer products.
Disadvantages:
- Brittleness: GPPS is not impact-resistant and is prone to breakage in high-impact environments.
- Low Heat Resistance: GPPS is sensitive to high temperatures and may deform under excessive heat.
General Purpose Polystyrene Crystal (GPPS) is an economical plastic material ideal for applications requiring transparency and rigidity. Its aesthetic and visual qualities make it a preferred material for projects focusing on appearance.
High Impact Polystyrene (HIPS)
High Impact Polystyrene, commonly known as HIPS, is a special type of polystyrene developed to enhance impact resistance. This material is produced by adding elastomers (rubber-like polymers) to rigid and brittle polystyrene, resulting in a combination of flexibility and durability, making it highly resistant to impacts.
Types of High Impact Polystyrene (HIPS):
- HIPS 6045
- HIPS 7026
- HIPS 7055
- HIPS 7240
Features of HIPS:
- High Impact Resistance: HIPS is highly resistant to mechanical impacts or hard surfaces, making it popular in the production of electronics and home appliances.
- Good Processability: HIPS is easy to shape and process, making it ideal for injection molding and thermoforming.
- Aesthetic Appearance: HIPS can be produced in a variety of colors and has a smooth, glossy surface.
- Economical: HIPS is more cost-effective than many other engineering plastics, making it suitable for a wide range of applications.
Applications:
- Electronics Products: Used in the casings for televisions, computers, and other electronic devices.
- Home Appliances: Exterior parts of refrigerators, washing machines, and other household appliances.
- Automotive: Interior components such as dashboards, panels, and other accessories.
- Toys: Preferred for the production of durable and safe toys.
High Impact Polystyrene (HIPS) combines the versatility of polystyrene with impact resistance, making it suitable for a broad range of industrial applications.
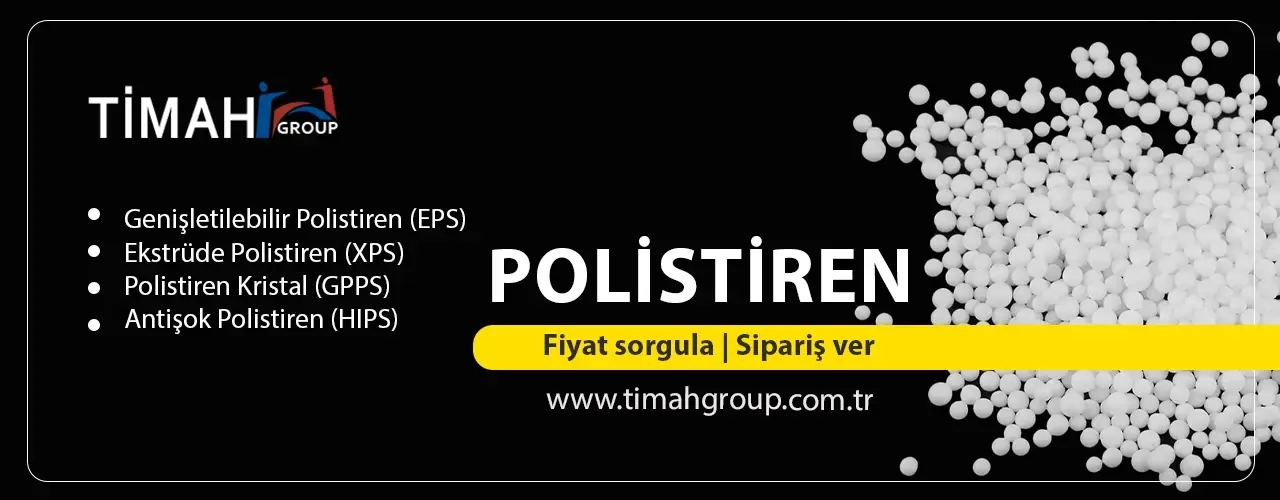